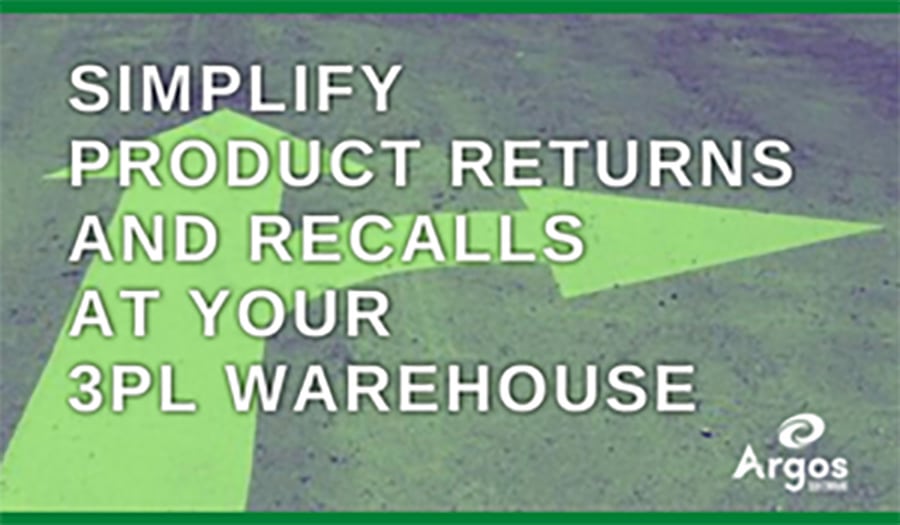
We live in the age of product returns. As a result, 3PL warehouses often receive returned inventory. Whether it be from a damaged shipment, item malfunction, or product recall, professional warehouse managers know that it is important to quickly process all returns. Yet, handling returns is labor-intensive, which drives up operational overhead.
What is the best way to process returns efficiently and keep those costs down while also maintaining overall customer satisfaction? The answer is…
to make sure you are using a quality warehouse management system (WMS) software. It has to have the ability to manage your inventory throughout its stock cycle and be easy to use, automating steps and integrating with external systems as needed to simplify and streamline the process.
The Best WMS Software Matters
Product recalls and returns do not have to be a pain for your 3PL warehouse. You can easily access real-time return data with the best software for warehouse management. This data allows for better decision-making in returns process management and increased productivity overall.
Your WMS software should always provide exceptional traceability and product information for each piece of inventory. Information often includes lot numbers and expiration dates. Receiving, picking, shipping and moving stock are all tasks that require accurate and fast data entry to stay abreast of real-time requirements which can be had through WMS generated RF barcodes and mobile readers. ABECAS Insight from Argos provides access to important data in an instant since the product expiration date and lot information is attached to each item’s bar code as it is received. Inventory bar codes are always scanned and available through your WMS software system, this way you can quickly access information on returned or recalled inventory at the facility including their internal location.
A well-managed 3PL warehouse logistics plan is very important when it comes to handling product recalls and returns. You can easily preplan incoming returns and inventory routes by using top-tier WMS software. Quality WMS software from Argos provides tracking on an individual inventory item basis while maintaining pre-set customer return standards. Plus, ABECAS Insight can work directly with your human resources system to schedule employees for returns and customize reports to track the workflow and labor hours assigned. In the end, your warehouse has the ability to make any necessary adjustments for future returns as needed based on information generated by the WMS system.
Instituting General Warehouse Return Guidelines
Your 3PL should have established general return guidelines, plus specific process requirements per customer. Most warehouses follow a standard set of procedures for returned goods. ABECAS Insight can store each step in the process for full inventory traceability.
1. Returned Inventory Procedures
A Return Merchandise Authorization (RMA) or Return Goods Authorization (RGA) form must be issued at the beginning of the returns process and can easily be generated through an online web portal. RGA/RMA information typically includes customer name, date of authorization, order number, and carrier tracking details. Once the warehouse receives the return, it is compared to the issued RMA/RGA for accuracy. Returned products should then be marked accordingly through user-defined fields in the WMS software and moved to a specified area for inspection.
2. Quality Inspection
All items returned to the warehouse should go through pre-defined quality inspection protocols that should include checking for carton and product issues. However, all food and beverages must be logged and disposed of since food items can never be resold once returned. If the packaging for non-food items is damaged and the product is not, that item can usually be repackaged and added back into the system for resale. Products that are damaged or noted as flawed can then be returned to the manufacturer or destroyed per customer instructions, recycling guidelines, and governing agency requirements.
3. Repack Product for Resale
When products are returned undamaged, a new SKU should then be assigned and noted as a previously returned product SKU. In some cases, these items may be offered at a discounted price by the supplier. Depending on a 3PL’s client agreement, repackaging can be done by the warehouse facility or the manufacturer.
Guidelines for Product Recalls
In many cases, recalled products are returned to 3PL warehouses or distribution centers. During recall processing, a warehouse must be able to provide complete life cycle information on all affected SKUs, including lot number(s) and expiration date(s). Warehouses must always be aware of what recalled inventory affects their facility, including how much each customer was shipped, quantities still on hand in-house, and how much recalled product will be returned to you. Recall guidelines need to include:
- Report on all recalled product shipments in the system to the client.
- Promptly place a hold on all affected SKUs. Products marked for recall should never be allocated or shipped, even if they are on the staging dock.
- Assign an isolated area of the facility for recalled inventory. It is best to indicate the area with appropriate signage and mark items with hold tags.
- Alert affected customers. Notification can come from the manufacturer or distributor depending on recall procedures. Communication with affected customers typically can be by email and may sometimes be accompanied by a press release.
- Additional recalled products from the manufacturer must be rejected at the dock even if they are on order.
- Class codes of any recalled SKU should be changed to aid in potential ordering, picking, receiving (returned), or destroyed under specified guidelines and regulations.
- Generate and issue required reports to the client.
- Some clients may want to conduct a mock recall as part of their warehouse partnership to ensure that a potential recall will run smoothly.
Identifying Trends in Returned Items
Your 3PL can also help identify return trends for your clients by utilizing the best software for warehouse management through customized report generation. Reports can include returned products, the reason for return, the date of return, and how often the same products have been sent back. This important information may help your clients identify potential recalls, uncover possible packaging or shipping problems, and highlight areas for future product improvements. The ability to provide this information generated by your WMS software gives your warehouse an advantage over the competition.
3PLs and warehouses can improve the overall return and recall process by following the above general guidelines and being proactive, which can save both you and the client time and money. If you want an improved way to manage product returns and recalls at your facility with the best software for warehouse management, it’s time to consider ABECAS Insight from Argos.