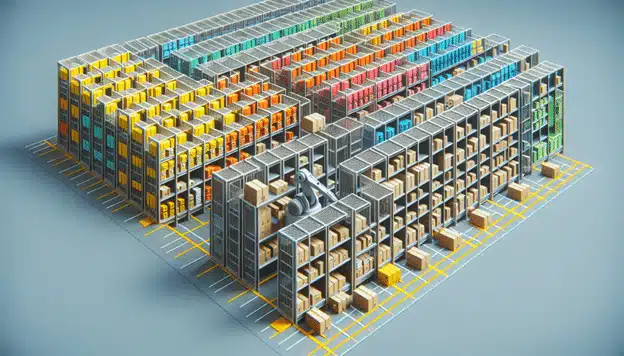
Struggling with warehouse organization? ‘Warehouse slotting’ might be your answer. It’s not just about orderly shelves; it’s a strategic, cost-saving decision that sharpens your operation’s efficiency and responsiveness. Dive into tools and tips to upgrade your warehouse layout, streamline your processes, and leverage slotting for notable operational improvement—with zero fluff.
Key Takeaways
- Warehouse slotting is vital for operational efficiency, aiming to maximize space utilization, minimize picking errors, and streamline workflow for improved handling and reduced costs.
- Slotting should be a strategic, data-driven process involving the creation of a blueprint based on item movement, inventory assessment, and warehouse layout, with consideration for special handling or storage requirements.
- Continuous improvement and real-time adjustments to the slotting strategy are necessary to adapt to market changes, while collaboration with warehouse workers and leveraging advanced WMS technologies can drive long-term success and operational optimization.
Unlocking the Power of Slotting in Your Warehouse
Picture this: A well-organized warehouse where every SKU has its place, and items flow smoothly from storage to dispatch. This is the vision of a warehouse powered by an effective slotting strategy. When the warehouse is organized for optimal product picking, the entire operation functions like a finely-tuned machine. Warehouse slotting ensures improved handling, reduced costs, and optimized storage, which cumulatively contribute to enhanced operational efficiencies.
The impact is not just on your operational metrics; it also ripples out to happier customers due to more reliable and on-time product deliveries.
The Essence of Slotting Strategy
In the heart of every efficient warehouse lies a robust slotting strategy. The systematic organization of inventory to ensure optimal storage and accessibility forms the backbone of operational efficiency. A well-structured slotting strategy plays a pivotal role in warehouse operations by providing:
- Peak optimization
- Enhanced productivity
- Streamlined workflow
- Significant efficiency and cost savings
Effective warehouse slotting incorporates key warehouse slotting strategies such as improving space utilization, reducing handling, and determining optimal SKU placement based on size, weight, and access frequency.
Key Objectives of a Robust Slotting Process
Slotting is not just about arranging items; it’s a strategic process with clear objectives. Increasing storage capacity by identifying and utilizing opportunities for current inventory storage optimization is a primary aim of a robust slotting process. It addresses complex challenges of balancing speed, safety, and efficient space utilization to maximize the utility of warehouse space.
Furthermore, it plays a significant role in reducing picking errors, streamlining warehouse operations, and minimizing mistakes. Minimizing the handling of inventory and improving inventory accuracy are essential objectives of an effective slotting process.
Related: Warehouse Inventory Management: Guide and Best Practices
Designing Your Slotting Blueprint: Where to Begin?
Designing a slotting blueprint involves the following steps:
- Understand item movement and storage needs by analyzing past sales data and unit velocity data.
- Assess the types of items in the product line and determine if sales involve individual items or larger quantities.
- Tailor the slotting approach to match the actual business operations.
By following these steps, you can create an effective slotting blueprint for your warehouse.
Special storage and handling requirements for items that are fragile or heavy also need to be considered for optimizing storage and inventory organization.
Analyzing Warehouse Space and Layout
Layout analysis is a pivotal step in designing your slotting blueprint. It involves evaluating the arrangement of pick zones and designing pathways for high throughput with minimal congestion. The placement of products should consider the type and weight, with heavy items placed at ground level and fragile items carefully slotted for safe handling. Special consideration areas, such as high-security or temperature-sensitive products, need careful planning to ensure compliance and safety. The ultimate goal is to achieve the maximum storage efficiency and capacity within the available space.
Inventory Assessment: Identifying All the SKUs
Inventory assessment, a crucial aspect of inventory management, is like taking a snapshot of the items in your warehouse. Key data points such as SKU data, item picking levels, and order history should be analyzed for effective slotting. Slotting best practices encompass considering data on item level, storage medium, cube size, weight, SKU velocity, and special storage requirements.
Detailed data for each SKU is required for an effective slotting approach. This data should take into account:
- Picking level
- Storage medium
- Cube size
- Weight
- Velocity
- Seasonal fluctuations
- Product affinity
Slotting Techniques for Optimizing Warehouse Operations
Slotting techniques are some of the best tools in your optimization toolkit. Organizing inventory based on seasonality and reducing product travel time are fundamental slotting strategies that contribute to a streamlined workflow. However, in today’s data-driven world, slotting optimization goes beyond the basics.
Slotting methods, such as ABC slotting, categorize items based on order frequency and guide their placement in the warehouse.
Macro Slotting Refers to Overall Layout Optimization
Macro slotting is all about seeing the big picture. It focuses on the strategic arrangement of pick zones for higher throughput. From the placement of heavy items at ground level to the careful slotting of fragile items for safe handling, every detail counts in macro slotting.
Even special consideration areas, such as high-security or temperature-sensitive products, are not left out in this process.
Micro Slotting: Fine-Tuning SKU Placement
Micro slotting, on the other hand, is about the finer details. It involves:
- The specific location of items within the zones
- Taking into account the interplay between fast-moving items and storage space
- Considering the level at which items are picked
- Considering the storage medium
- Considering item size, weight, and special storage requirements
Every aspect is considered in micro slotting.
Advanced Slotting Technologies: Leveraging WMS Capabilities
In the realm of warehouse operations, technology is a game-changer. A warehouse management system (WMS) plays a central role in enhancing slotting optimization, leveraging real-time data to reduce picking errors and scale operations efficiently in a warehouse or distribution center.
Advanced simulation tools offered by some systems enable managers to visualize slotting changes and utilize planning features for real-time warehouse layout optimization via macro slotting.
Cutting-Edge Features of Warehouse Management Software
The cutting-edge features of warehouse management software simplify the slotting process. Automated SKU velocity calculation, mobile picking technologies, and visual representations of warehouse space are just a few examples. The software can profile products by attributes such as size, weight, and demand for improved slotting.
And, the best part? You can even customize slotting rules in a WMS to ensure safe and optimal placement of special categories like hazardous materials or fragile items.
Integrating Slotting Algorithms for Precision
Precision is key in warehouse operations, and slotting algorithms provide just that. The ABC method, for instance, assists managers in categorizing items based on their movement speed, promoting efficient placement by prioritizing high-velocity SKUs.
Predictive analytics in advanced WMS software utilizes both market trends and historical data to forecast future SKU movement, offering a strategic approach to micro slotting adjustments.
Related: Mastering 3PL Inventory Management: A Comprehensive Guide
Streamlining the Picking Process with Strategic Slotting
Streamlining the picking process is one of the significant advantages of strategic slotting. Remember that the most time-consuming part of the order picking process is traveling, which takes up approximately 55% of a picker’s time. Efficiently slotted warehouses can significantly minimize search and travel time, enhancing productivity.
Fast-Moving vs. Slow-Moving Items: A Balancing Act
In an entire warehouse, not all items move at the same pace. Segregating fast-moving from slow-moving warehouse inventory can lead to significant increases in productivity, space usage, and stock utilization.
Fast-moving items are generally low-cost and have high turnover, while slow-moving items can result in wasted capital and resources if not slotted efficiently.
The Role of SKU Velocity in Pick Path Optimization
SKU velocity plays a significant role in optimizing pick paths and enhancing warehouse operations. Products are classified by SKU turnover speed into quickly sold ‘A’ items, average ‘B’ items, or slow-moving ‘C’ items.
High-velocity ‘A’ SKUs are strategically stored close to dispatch areas in the distribution center to minimize travel distance and picking times.
Warehouse Slotting Best Practices for Long-Term Success
Warehouse slotting is not a one-time task; it requires continuous effort and improvement for long-term success. It is necessary to revisit warehouse slotting regularly for continuous improvement in selection and replenishment labor practices.
Regular Reassessment to Adapt to Market Changes
Just like changing market trends, your warehouse slotting strategy should also be flexible enough to adapt. Slotting plans need continuous monitoring and improvement, with frequent analyses and real-time adjustments being key to optimized order fulfillment.
Seasonality can significantly affect item demand, necessitating appropriate adjustments in the warehouse layout and slotting configurations to optimize for peaks in SKU velocity during various times of the year.
Collaboration with Warehouse Workers for Continuous Improvement
Warehouse workers are the ones on the ground, and their insights can provide valuable feedback to improve your slotting strategy. Regular inclusion of feedback from pickers can provide unique insights into the efficiency and effectiveness of the current warehouse organization.
Transforming Unused Warehouse Space into Profitable Real Estate
Unused warehouse space represents a goldmine of opportunities, not merely wasted space. Utilizing smart slotting strategies in the warehouse can lead to increased storage capacity and delay the need for expansion, saving on warehousing costs.
Navigating the Challenges of Warehouse Slotting
Like every process, warehouse slotting presents its own unique challenges. Balancing the slotting of items based on sales volume with an awareness of traffic flow can prevent bottlenecks and congestion within the warehouse.
Avoiding Traffic Jams and Maximizing Floor Space
Avoiding traffic jams and maximizing floor space are two key challenges in warehouse slotting. High-demand items should be grouped in sections that do not interfere with the workflow of other pickers, ensuring that traffic jams are minimized.
Overcoming Resistance: Convincing Stakeholders of Slotting Benefits
In any organizational process, resistance to change is a common hurdle. Introducing a slotting process in the warehouse can encounter resistance from stakeholders. Therefore, it’s crucial to highlight the potential benefits of warehouse slotting, including increased safety, faster picking, and reduced carrying costs.
Summary: Elevate Your Warehouse Efficiency with Argos Software
In conclusion, the strategic implementation of warehouse slotting principles is essential for any business seeking to enhance operational efficiency, reduce costs, and improve customer satisfaction. Argos Software offers cutting-edge Warehouse Management System (WMS) solutions tailored to streamline your warehouse operations, from optimizing slotting processes to leveraging real-time data for informed decision-making.
Discover how Argos Software can transform your warehouse into a model of efficiency and productivity. Contact us today to explore our solutions and learn how we can help you achieve your operational goals.
Unlock the full potential of your warehouse with Argos Software. Contact us to learn more.
Frequently Asked Questions
What is the slotting technique?
The slotting technique aims to increase warehouse functionality by organizing to maximize space and make picking more efficient, ultimately reducing wasted travel and increasing pick density.
How does slotting work?
Slotting in a warehouse involves strategically organizing inventory to optimize accessibility, picking speed, accuracy, and storage capacity. It aims to make fulfillment and replenishment as efficient as possible.
What is dynamic slotting in a warehouse?
Dynamic slotting is a technique used in warehouse management to track SKU inventory counts in each bin location and add new bin locations as needed, often accommodating variability in product turnover rates. This method allows for more efficient use of space and resources in the warehouse.
What is slotting optimization?
Slotting optimization is the process of assigning each SKU to its most productive location within the distribution center, improving efficiency and reducing labor costs.
What is warehouse slotting?
Warehouse slotting is the process of organizing a warehouse to improve product picking efficiency.