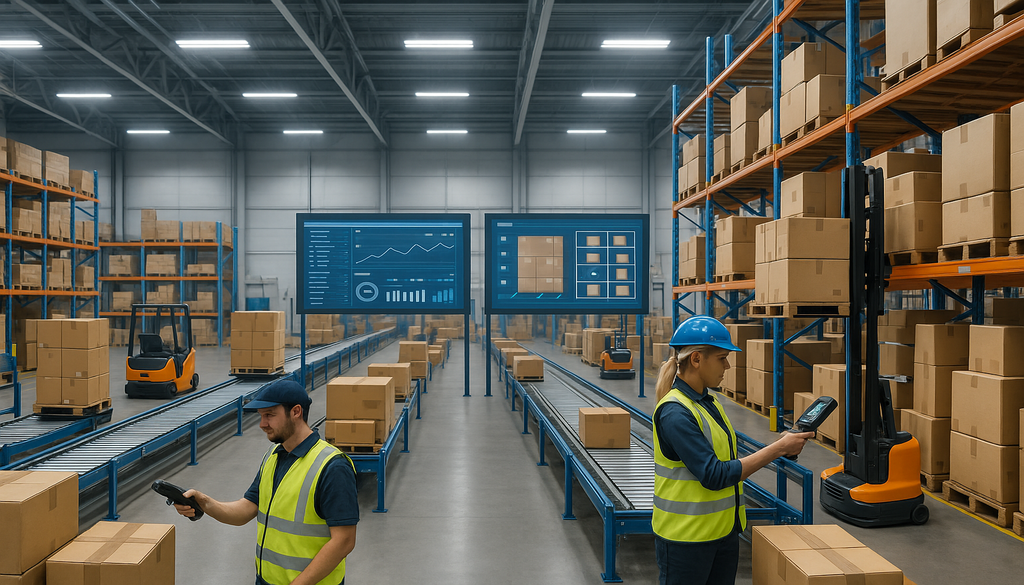
Introduction
In today’s fast-paced supply chain landscape, the accuracy of your warehouse inventory can make or break your operational efficiency. With rising customer expectations and increasingly complex logistics networks, businesses can no longer afford to rely on manual or outdated inventory tracking methods. Effective warehouse inventory tracking systems are essential for reducing errors, optimizing stock levels, and ensuring timely order fulfillment. In this article, we’ll explore seven essential tips for leveraging these systems to their fullest potential. Whether you’re upgrading your current processes or implementing a new solution, these insights will help you achieve greater precision and reliability in your warehouse operations.
Understanding the Basics of Warehouse Inventory Tracking Systems
Warehouse inventory tracking systems are the backbone of modern warehouse management, providing real-time visibility into stock levels, locations, and movements. At their core, these systems use a combination of software and hardware to monitor inventory as it moves through receiving, storage, picking, packing, and shipping. By automating data capture and reducing manual entry, inventory tracking systems help minimize errors and streamline workflows.
The primary role of these systems is to ensure that every item in the warehouse is accounted for, from the moment it arrives until it leaves the facility. This is achieved through unique identifiers—such as barcodes, RFID tags, or serial numbers—that are scanned and recorded at each touchpoint. As a result, warehouse managers gain up-to-date insights into stock availability, reducing the risk of overstocking or stockouts. Additionally, these systems support better decision-making by providing accurate data for forecasting, replenishment, and performance analysis.
Choosing the Right Warehouse Inventory Tracking Software
Selecting the right inventory tracking software is a critical decision that can impact every aspect of warehouse operations. The ideal solution should align with your warehouse’s size, complexity, and specific business needs. Key factors to consider include scalability, integration capabilities, user interface, and support for automation technologies like barcoding or RFID. It’s also important to evaluate the software’s reporting and analytics features, as these will be essential for ongoing optimization.
When assessing potential solutions, start by mapping out your current workflows and identifying pain points that the software should address. For example, if your warehouse handles a high volume of SKUs or requires multi-location tracking, look for systems that offer robust inventory categorization and location management. Additionally, consider the ease of integration with existing systems such as ERP, WMS, or e-commerce platforms. Conducting a thorough needs assessment and involving key stakeholders in the selection process will help ensure the chosen software delivers long-term value and supports your growth objectives.
Implementing Barcode and RFID Technology
Barcoding and RFID (Radio Frequency Identification) technologies are among the most effective tools for improving inventory tracking accuracy and efficiency. Barcodes are widely used due to their simplicity and low cost, enabling quick scanning and data entry at every stage of the inventory lifecycle. RFID, on the other hand, offers advanced capabilities by allowing multiple items to be scanned simultaneously and without direct line-of-sight, making it ideal for high-volume or high-value inventory environments.
To successfully integrate these technologies, start by evaluating your inventory types and operational requirements. Begin with a pilot program in a specific area of the warehouse to test the technology and refine your processes. The implementation process typically involves labeling all inventory items with barcodes or RFID tags, equipping staff with handheld scanners or RFID readers, and configuring your inventory tracking software to capture and process the data. Training staff on proper scanning techniques and establishing clear protocols for tag placement and maintenance are also crucial for long-term success. By combining these technologies with robust software, warehouses can achieve near real-time inventory visibility and significantly reduce manual errors.
Regular Audits and Data Reconciliation
Regular inventory audits and data reconciliation are essential for maintaining the accuracy and integrity of your warehouse inventory records. Even with advanced tracking systems, discrepancies can arise due to mis-scans, misplaced items, or process lapses. Periodic audits—whether cycle counts or full physical inventories—help identify and correct these issues before they escalate into larger problems.
Best practices for effective data reconciliation include establishing a consistent audit schedule based on inventory turnover rates and risk factors. For high-value or fast-moving items, more frequent cycle counts may be necessary. Use audit results to investigate root causes of discrepancies and implement corrective actions, such as retraining staff or refining standard operating procedures. Leveraging your inventory tracking system’s reporting tools can streamline the reconciliation process by highlighting variances and generating actionable insights. Ultimately, regular audits not only improve inventory accuracy but also build trust with customers and stakeholders by ensuring reliable order fulfillment.
Training Staff on Inventory Tracking Best Practices
A warehouse inventory tracking system is only as effective as the people who use it. Comprehensive staff training is critical to ensure that employees understand the importance of accurate data entry, proper use of technology, and adherence to established processes. Key training topics should include system navigation, barcode or RFID scanning procedures, handling exceptions, and troubleshooting common issues.
Ongoing education and support are equally important, as warehouse operations and technologies continually evolve. Consider implementing refresher courses, hands-on workshops, and digital training resources to keep staff up-to-date with best practices. Encourage a culture of accountability and continuous improvement by recognizing employees who demonstrate exceptional accuracy and efficiency. By investing in staff training, warehouses can minimize errors, boost productivity, and maximize the return on their inventory tracking system investment.
Utilizing Data Analytics for Inventory Optimization
Data analytics is a powerful tool for transforming raw inventory data into actionable insights that drive operational improvements. Modern inventory tracking systems generate vast amounts of data on stock levels, movement patterns, and order histories. By analyzing this data, warehouse managers can identify trends, forecast demand, and optimize inventory replenishment strategies.
For example, analytics can reveal slow-moving items that tie up valuable storage space or highlight peak periods that require additional staffing. Advanced systems may offer predictive analytics, enabling proactive decision-making and reducing the risk of stockouts or overstocking. Visualization tools such as dashboards and heatmaps make it easier to interpret complex data and communicate findings to stakeholders. By leveraging analytics, warehouses can continuously refine their processes, reduce carrying costs, and improve customer satisfaction through more accurate and timely order fulfillment.
Adapting to Changing Inventory Needs
The ability to adapt to changing inventory requirements is essential for long-term warehouse success. As businesses grow, diversify their product lines, or enter new markets, inventory tracking systems must be flexible and scalable. Start by choosing solutions that support modular upgrades and can handle increased transaction volumes without sacrificing performance.
Regularly review your inventory tracking processes to ensure they remain aligned with business objectives and market conditions. For instance, if your warehouse begins handling perishable goods or high-value items, you may need to implement additional tracking features such as temperature monitoring or enhanced security protocols. Stay informed about emerging technologies and industry best practices to remain agile in the face of change. By proactively adjusting your inventory tracking strategies, you can support business growth, respond to customer demands, and maintain a competitive edge in the marketplace.
Conclusion
Effective warehouse inventory tracking is a cornerstone of operational excellence in today’s supply chain environment. By understanding the fundamentals, selecting the right software, leveraging barcode and RFID technology, conducting regular audits, investing in staff training, utilizing data analytics, and remaining adaptable, warehouse managers can achieve greater accuracy and efficiency. These seven essential tips provide a roadmap for optimizing your inventory tracking systems and driving continuous improvement. Take the next step by evaluating your current processes and implementing these strategies to enhance your warehouse performance and customer satisfaction.
Frequently Asked Questions (FAQ)
Q1: What are the common challenges in warehouse inventory tracking?
A1: Common challenges in warehouse inventory tracking include data entry errors, lack of real-time updates, and difficulties in tracking items across multiple locations. Additional issues may involve misplacement of goods, discrepancies between physical and recorded inventory, and integration problems with other business systems. Addressing these challenges requires robust tracking technologies, regular audits, and comprehensive staff training.
Q2: How often should warehouse inventory audits be conducted?
A2: The frequency of warehouse inventory audits depends on factors such as inventory size, turnover rate, and the value of goods stored. Generally, it is recommended to conduct audits quarterly or bi-annually. However, high-turnover or high-value warehouses may benefit from more frequent cycle counts, such as monthly or even weekly, to ensure ongoing accuracy and minimize discrepancies.
Q3: Can warehouse inventory tracking systems integrate with other business management software?
A3: Yes, most modern warehouse inventory tracking systems are designed to integrate seamlessly with other business management platforms, such as ERP (Enterprise Resource Planning) and WMS (Warehouse Management Systems). This integration provides a unified view of operations, streamlines workflows, and enhances data accuracy across the organization, enabling better decision-making and improved efficiency.
Q4: What is the impact of inaccurate inventory tracking on a business?
A4: Inaccurate inventory tracking can have significant negative impacts on a business, including overstocking or stockouts, increased operational costs, and poor customer service. These issues can lead to lost sales, excess carrying costs, and damaged reputation. Maintaining accurate inventory records is essential for efficient operations, cost control, and customer satisfaction.
Q5: Are there mobile solutions for warehouse inventory tracking?
A5: Yes, many inventory tracking systems offer mobile applications that enable staff to update and access inventory data from anywhere within the warehouse. Mobile solutions improve flexibility, support real-time data entry, and enhance overall productivity by allowing employees to perform inventory tasks on handheld devices or tablets, reducing reliance on stationary workstations.